The Role of LIMS in the Shopfloor IT Landscape
Laboratory Information Management Systems (LIMS) are an important part of lean manufacturing and swift product release: A LIMS drives quality throughout the manufacturing flow by managing and tracking the samples of raw materials, intermediate and final product, ensuring they can be quickly related to the relevant product and batch. LIMS helps you automate and control your sample testing, and record data results, to conform to regulatory requirements - making production seamless and efficient.
The (typical) Production-IT environment
Most products produced require some form of testing to be released for shipping to the customers. In many cases testing is performed in an on-site laboratory. Wherever this is the case, sampling and sample handling is one important step in the overall process. How to ensure that data is captured without errors in an organized manner and with various people involved across multiple departments?
Typically, a production driven process tends to see analytics as a necessary side business which often leads to the fact that it is tried to integrate these requirements in the production systems already used - such as ERP or MES. However, if analytical requirements get more complex a dedicated LIMS is normally a much better option. For quality it typically comes with build in functions off the shelf that are needed to ensure a good quality control. Equipment interfaces, sampling plans, calibration management and test method management are just some examples.
Core functionality vs. development effort
A system usually shines in the field it was designed for but needs some serious work to be adapted to processes it was not intended for. In terms of maintenance and development one must consider that effort increases exponentially the further away from the initial off-the-shelf solution the requirement is. This is true if developments are done in-house and for extensions done by the software vendor.
There are many ERP or MES Systems out there that advertise with capabilities usually a LIMS would compete for. Usually, once faced with a complex process of the laboratory area, these systems quickly show limitations. They might very well be acceptable for smaller businesses for the sake of a simple IT landscape but certainly for bigger production organizations, the utilization of a dedicated LIMS should be considered.
Integrating a LIMS into a production environment
Let us assume a manufacturing company has a MES and an ERP installed and now wants to enhance the quality area by a implementing a dedicated LIMS. The goal should be to manage the systems in a way where a normal user only works in one system to do his daily job. There are two main reasons for this approach. Each manual lookup of data or the management of data independently in different systems is error prone and for a user to constantly switch systems can become frustrating. On the other hand, work in one system cannot be done without data from another system as the following examples show.
Handshakes
- Quality release of a campaign usually requires check of production data as well as lab results.
- Sampling: Usually production needs to know what samples to take and QC needs to ensure that samples are taken. Samples must carry data that makes them identifiable in both systems.
- Testing based on a sampling plan may require tests performed at the line (normally by production) and tests performed off the line (in a lab).
To resolve these situations the requirement for interfaces arises. Interfaces always should be as few as possible and simplified in order to achieve a stable and sustainable process. But, as we are in a modern full digital environment, we should not be afraid of interfaces in general. Modern systems often come with supporting tools that minimize the effort of interface developments. The key goal should be to limit the connections while leveraging the core functionalities of the individual systems as much as possible.
What could be a good process-driven landscape in a shop floor environment between the three typical systems?
Let us have a look at the core “tasks“ ERP, MES and LIMS are typically designed for:
- ERP: Typically leading System for Master Data (such as Material, Customers, Vendors…) planning and inventory.
- MES: Leading System for production execution control and production “actual“ data.
- LIMS: Leading System for Quality Master Data and Release
From there we can easily draw a map of interfaces that are required to achieve the goals mentioned above: Normally in an ERP System where the planning starts, a production order is generated and typically released to production. This information which normally does not consist of more then order no. , dates, order size and target material, is typically already transferred to MES Systems for further execution. But what if it is also relayed to LIMS at the same time and we can use it there to generate all necessary samples as per product specific sampling plan. Samples can be categorized into samples to be taken from production and samples to be analyzed by the laboratory. These sometimes can be the same, but often as sample preparation is required are different. Sampling information can then be relayed to the MES System as to notify production what and when to take samples. Once a batch/campaign testing is completed a quality release is done by QC department and send back to the ERP System.
A complete landscape example with the necessary interfaces
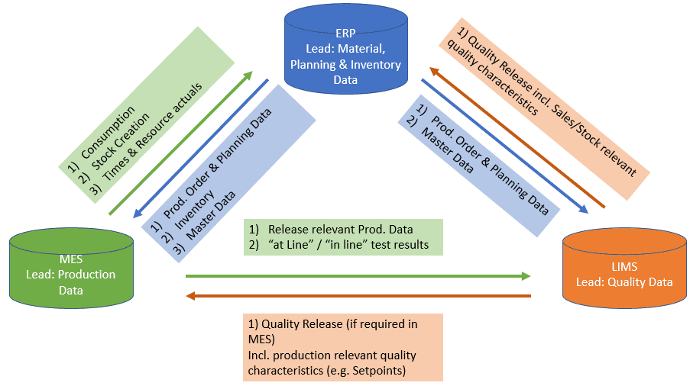
LIMS in a Shop Floor IT Landscape